Hard chrome plating is part craft, part science.
Working with chrome requires technical proficiency combined with intuitive knowledge. It requires an intimate understanding of the behavior of different components and materials.
Years of experience is required to work with materials where tolerances are tight and often the standards quality is measured in microns. These are complex crafts that cannot be learned in a textbook and can only be mastered through repeated practice acquired through years of working with the material.
The secret to this consistency is pride. Every job that enters our facility is treated with the same level of professional attention. From inspection and evaluation, to stripping, plating, and finishing, we maintain strict quality control over the entire process until the product is delivered to the customer.
> Part One: Inspection
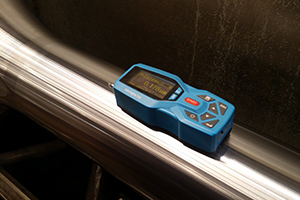
In the initial inspection, the object to be plated is assessed to evaluate its condition ahead of the chroming process. We look for evidence of corrosion, pitting, marring, damage, cracking or flaking of the material. Presence of these phenomena will be taken into account and may influence the decisions taken at various steps along the re-chroming process.
> Part Two: Stripping / Grinding
In order to prevent defects, all trace of worn chrome must be removed before the object can be plated.
For this purpose, CCA operates a number of stripping and grinding facilities to accurately remove old chrome material without affecting the base metal.
During stripping, the rod is placed in a reverse-electrolysis tank. A negative current is applied to the solution and chrome molecules separate from the surface – thereby stripping the old chrome away.
During the grinding process, the rod is centered on a large lathe-like grinding machine and brought into contact with the spinning stone grinding wheel. This technique requires a high level of skill and experience from the operator who must instinctively gauge how much pressure to apply to remove the layer of chrome without damaging the steel underneath.
> Part Three: Cleaning / Masking
Every object to be plated must be thoroughly cleaned to remove any debris or contaminants must be removed. The presence of which could lead to undesirable anomalies such as pitting and pinholes or flaking and peeling of the chrome during the life of the cylinder. At this stage, the object is also masked to ensure a neat and professional final product.
> Part Four: Framing / Jigging
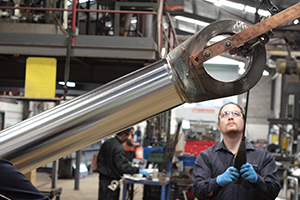
Current density is all important when it comes to achieving a consistent result, which is why correct framing is essential in order for chrome build up to take place evenly.
At this stage, the technician takes care to build the correct frame around the object to be plated. This is where experience plays a role in determining the outcome. CCA’s knowledgeable technicians employ years of practice to correctly position and frame the object to ensure each part of the component receives the same amount of current. Failing to do this would result in either missed spots or patches of high deposits and / or milky or burnt chrome defects.
> Part Five: Electroplating
Objects to be plated are placed in a bath containing a chromium solution. Electrodes are attached to the object to be plated and a positive current is applied. This causes the dissolved chrome particles in the solution to be attracted to and adhere to the steel surface of the object.
Precisely the right amount of current must be delivered at a steady rate whilst bath chemistry and temperature are maintained for the duration of the plating process. Any interruptions in power will disrupt the consistent layering of chrome deposits and result in defects such as flaking, which could cause the cylinder to perform poorly or fail soon after repair.
> Part Six: Post Grinding
In some cases, post grinding must take place in order to return the object to the correct dimensions to ensure it meets the specified tolerances for the application. Stone grinding is used to reduce the surface thickness to the required specification.
As specialists in hard chrome for industrial applications, we understand the engineering requirements for precise components. As such, we employ our knowledge and experience during post grinding to remove the correct amount of build-up before final surface finishing.
> Part Seven: Linishing
Linishing is the process of applying the correct surface finish for the application. This is extremely important in most industrial applications where surface texture is used to create the right friction properties.
Linishing creates microscopic striations which fill with fluid during operation to provide a silky smooth layer of oil upon which the seal may run. This reduces the friction and abrasive forces and dramatically improves the performance and lifespan of the cylinder.
Once again, CCA’s technicians put their skill and experience to work to achieve the correct surface finish. The rod is centered on a large lathe-like linishing machine, which spins the rod at a constant rate while differing grades of linishing belts are used to finely sand the chrome surface to the perfect thickness and consistency. Berendsen has two such linishing machines, which are big enough to accommodate large scale cylinders found on cranes and heavy mining machines.
Inspection | In the initial inspection, the object to be plated is assessed to evaluate its condition ahead of the chroming process. We look for evidence of corrosion, pitting, marring, damage, cracking or flaking of the material. Presence of these phenomena will be taken into account and may influence the decisions taken at various steps along the re-chroming process. |
---|---|
Stripping / Grinding | In order to prevent defects, all trace of worn chrome must be removed before the object can be plated.
For this purpose, CCA operates a number of stripping and grinding facilities to accurately remove old chrome material without affecting the base metal. During stripping, the rod is placed in a reverse-electrolysis tank. A negative current is applied to the solution and chrome molecules separate from the surface – thereby stripping the old chrome away. During the grinding process, the rod is centered on a large lathe-like grinding machine and brought into contact with the spinning stone grinding wheel. This technique requires a high level of skill and experience from the operator who must instinctively gauge how much pressure to apply to remove the layer of chrome without damaging the steel underneath. |
Cleaning / Masking | Every object to be plated must be thoroughly cleaned to remove any debris or contaminants must be removed. The presence of which could lead to undesirable anomalies such as pitting and pinholes or flaking and peeling of the chrome during the life of the cylinder. At this stage, the object is also masked to ensure a neat and professional final product. |
Framing / Jigging | Current density is all important when it comes to achieving a consistent result, which is why correct framing is essential in order for chrome build up to take place evenly.
At this stage, the technician takes care to build the correct frame around the object to be plated. This is where experience plays a role in determining the outcome. CCA’s knowledgable technicians employ years of practice to correctly position and frame the object to ensure each part of the component receives the same amount of current. Failing to do this would result in either missed spots or patches of high deposits and / or milky or burnt chrome defects. |
Electroplating | Objects to be plated are placed in a bath containing a chromium solution. Electrodes are attached to the object to be plated and a positive current is applied to This causes the dissolved chrome particles in the solution to be attracted to and adhere to the steel surface of the object.
Precisely the right amount of current must be delivered at a steady rate whilst bath chemistry and temperature are maintained for the duration of the plating process. Any interruptions in power will disrupt the consistent layering of chrome deposits and result in defects such as flaking, which could cause the cylinder to perform poorly or fail soon after repair. |
Post grinding | In some cases, post grinding must take place in order to return the object to the correct dimensions to ensure it meets the specified tolerances for the application. Stone grinding is used to reduce the surface thickness to the required specification.
As specialists in hard chrome for industrial applications, we understand the engineering requirements for precise components. As such, we employ our knowledge and experience during post grinding to remove the correct amount of build-up before final surface finishing. |
Linishing | Linishing is the process of applying the correct surface finish for the application. This is extremely important in most industrial applications where surface texture is used to create the right friction properties.
Linishing creates microscopic striations which fill with fluid during operation to provide a silky smooth layer of oil upon which the seal may run. This reduces the friction and abrasive forces and dramatically improves the performance and lifespan of the cylinder. Once again, CCA’s technicians put their skill and experience to work to achieve the correct surface finish. The rod is centered on a large lathe-like linishing machine, which spins the rod at a constant rate while differing grades of linishing belts are used to finely sand the chrome surface to the perfect thickness and consistency. Berendsen has two such linishing machines, which are big enough to accommodate large scale cylinders found on cranes and heavy mining machines. |
Want to learn more about how CCA Hardchrome can assist you with your chroming needs?